What is CAD Design and 3d Printing?
CAD (Computer-Aided Design) is a powerful tool for designing three-dimensional objects, and 3D printing has made it possible to create physical objects from CAD designs. So, the most important thing to remember while designing for 3D printing is the fact that your digital design will become a physical object.
Creating a CAD design that is printable requires more than just design skill as not all CAD designs are printable. There are certain considerations that need to be taken into account to ensure a successful 3D print. It requires an understanding of the principles of 3D printing and the limitations of the specific printer that will be used.
Anything can be “drawn” in 3D on digital software, but not everything can be 3D printed. Knowing the key factors that go into designing 3D models will ensure that you produce digital designs that can be successfully printed. Here are some key points to keep in mind when designing for 3D printing.
5 Things to Know Before Designing for 3D Printing
1. Warping
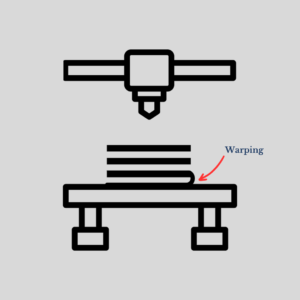
One of the key considerations in designing a 3D printable object is warping. Warping is a phenomenon where the edges of the print curl up or the print detaches from the bed during printing. The product during the printing process may be melted, sintered, or scanned with a laser and solidified which makes especially larger parts much more prone to warping.
This can be caused by a variety of factors, including the type of material used, the printer’s temperature settings, and the geometry of the model. To minimize warping, designers need to ensure that the design has a large base that can be adhered to the print bed, the printer bed is level, the print bed is heated to the correct temperature, and the temperature and humidity of the printing environment are controlled. Correct machine calibration and having adequate surface adhesion between your part and the print bed help in avoiding warping.
2. Overhangs
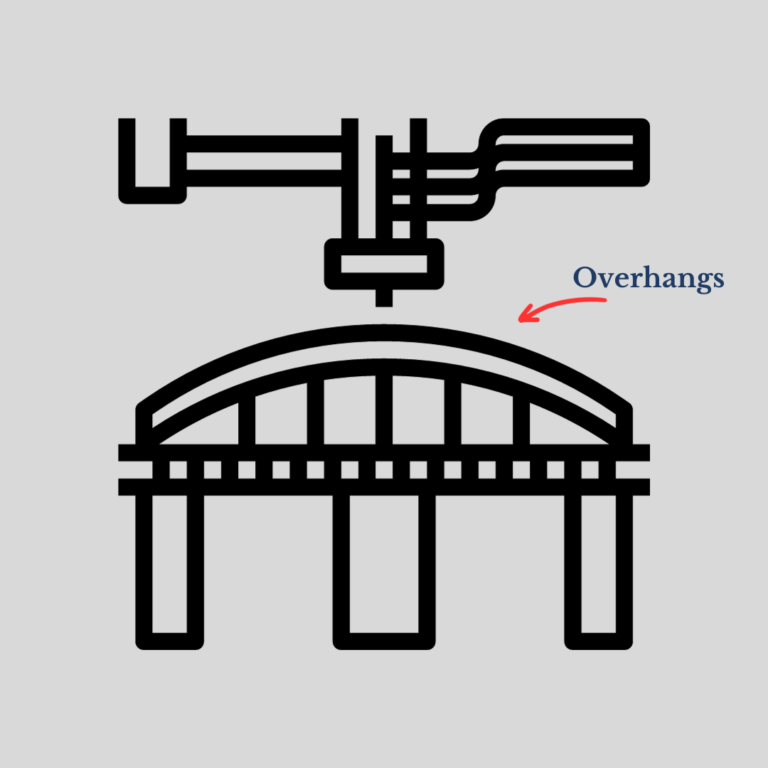
When designing a 3D model, it is important to consider the model’s overhangs, which are the sections of the model that extend beyond the previous layer without any support. If the designed object is in the air at an angle above 45 degrees, the printed model tends to overhang, which can cause the print to fail.
To avoid this, designers need to add support structures, which are temporary structures that support the overhangs while printing. Support structures can be automatically generated by CAD software, or they can be manually added by the designer.
However, support structures usually come out with a rougher surface finish. Reducing the speed of printing and the use of high-speed fans can prove to be helpful.
3. Minimum thickness
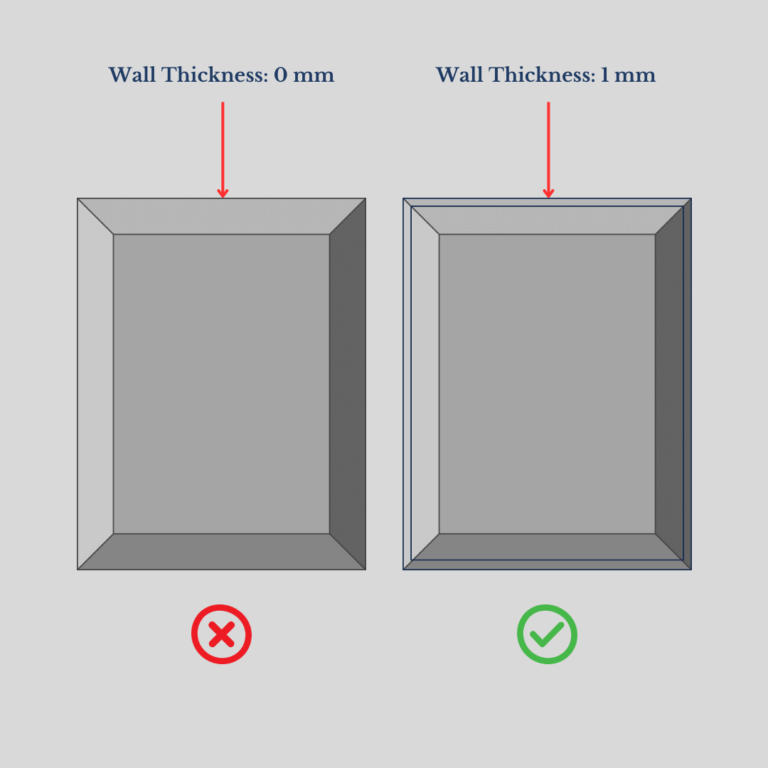
Minimum thickness is also an important consideration in designing 3D printable models. The minimum thickness required for a printable object depends on the printer’s resolution and the material used. If the thickness is too small, the printer may not be able to print the object accurately, resulting in a low-quality print or a failed print.
Each printing process has different tolerances like FDM, for instance, is the least accurate, while SLA has the tightest tolerance. All 3D printers can successfully print components with wall thicknesses greater than 0.8 mm. If the wall thickness is less than 0.8 mm then the layers will not be attached to the object and parts will come out easily.
4. Minimum feature size
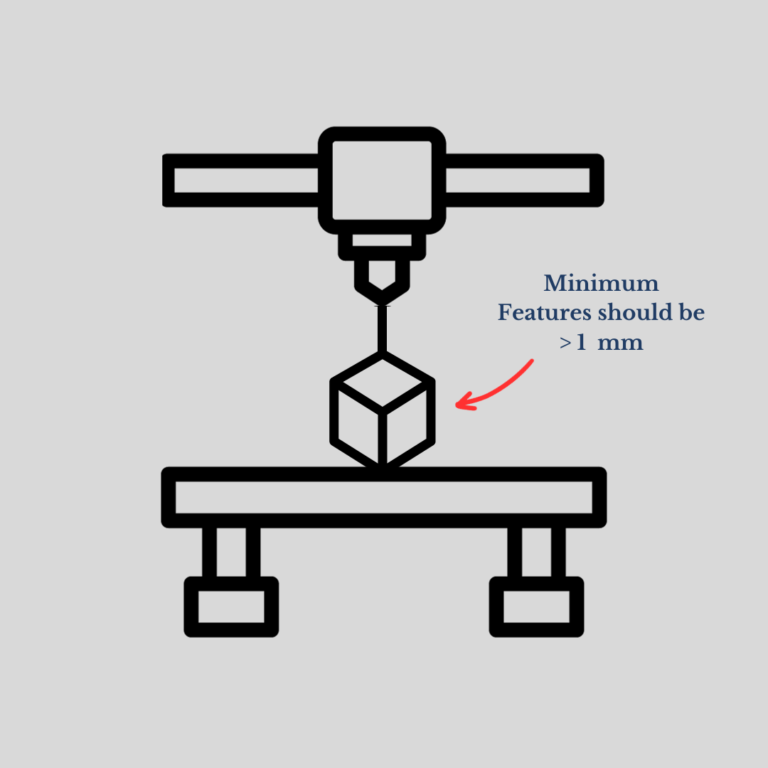
Similar to a minimum thickness, the minimum feature size required for a 3D print will depend on the material and printer being used. If the feature size is too small, the printer may not be able to print the feature accurately. For small details in the design, the process and materials which satisfies the requirement should be selected.
However, the details in a design somewhat slow down the printing process, so these factors should be considered before printing the 3D model. It is important to design the model with features that are within the printer’s capabilities to ensure a successful print.
5. Correct machine calibration
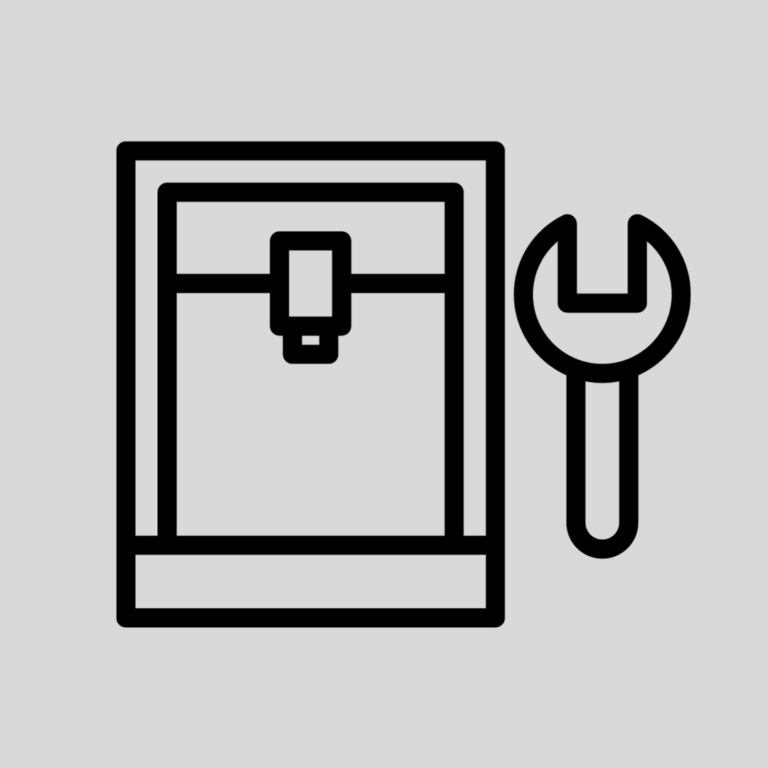
Machine calibration is crucial for a successful 3D print. If the printer is not calibrated correctly, the printed object may be distorted or inaccurate. Calibration involves adjusting the printer’s settings to ensure that it is printing accurately and consistently. This includes adjusting the printer’s bed level, temperature, and nozzle height.
The printer must be properly calibrated to ensure accurate printing and prevent issues such as layer shifting or print skewing. Real-life examples of CAD designs for 3D printing include custom phone cases, replacement parts for machinery, and even prosthetics. In each of these cases, designers needed to take into account the specific requirements of 3D printing, such as warping, overhangs, minimum thickness and feature sizes, and machine calibration, in order to create a successful 3D printable design.
Conclusion
In conclusion, designing CAD models for 3D printing requires careful consideration of a variety of factors. These are just a few considerations to keep in mind when designing for 3D printing. Other factors, such as material selection and print orientation, also play a role in the success of a 3D print. By taking these considerations into account, you can ensure that your CAD designs are optimized for 3D printing and that your final product meets your expectations.